A Comparative Study of Small-Diameter Copper Tubes with LU-VE With growing concerns about...
Motivations for New Heat Exchanger Design
Motivation for new HVAC/R equipment design often stems from many factors. There's a concerted effort towards emission reduction, aligning with stringent EPA policies to safeguard the environment.
Refrigerant transitions are imperative to comply with evolving emissions regulations and decarbonization agendas. The dynamic landscape necessitates continual adaptation to meet current requirements, with further changes anticipated. However, switching refrigerants poses numerous HVAC/R system design hurdles, affecting system performance and component selection.
Energy efficiency standards are a paramount concern, driving innovation towards systems that perform well and do so with minimal energy consumption. Additionally, there's a keen focus on gaining a competitive edge in the market, whether by introducing new functionalities, streamlining costs, or achieving both simultaneously. This combination of environmental responsibility, technological advancement, and market insight propels the evolution of HVAC/R equipment design into constant innovation and improvement.
According to the Engineering Team at OTS R&D, Inc., there are three driving factors motivating new product design:
- Energy efficiency, including:
-
- Equipment standard legislation
- End-user operational savings
- Emissions reductions are driven by:
- Environmental legislation
- Decarbonization initiatives
- Customer or market advantage involving:
- New functionality
- Cost reductions
New Product Design
When transitioning to new refrigerants in product design, the primary consideration revolves around determining if the change warrants a complete overhaul of the existing product design. This assessment hinges on the extent of the impact of the refrigerant transition. If deemed substantial, the focus shifts towards the heat exchangers. Heat exchangers emerge as pivotal elements in overcoming these challenges.
Addressing concerns such as flammability and toxicity entails limiting refrigerant charge volumes while enhancing capacity and efficiency demands by optimizing heat exchanger configurations to minimize expenses. Incorporating small-diameter copper tubes has several benefits, which become evident in these scenarios. Small-diameter copper offers enhanced efficiency and compatibility with various and new refrigerants, facilitating more streamlined HVAC/R redesigns and ensuring optimal performance amidst evolving industry standards.
Procrastination
Meeting the new standards seems imperative; nevertheless, manufacturers frequently delay these adaptations due to time constraints, expectations of changing standards, or resource limitations, resulting in a decline in market competitiveness. Martin acknowledges the intricacies of aligning various industry sectors, including refrigerant manufacturers, OEMs, and compressor manufacturers. Concerted efforts from all stakeholders are imperative to propel the industry toward progress.
How can companies manage performance losses resulting from last-minute alterations? Companies could still fulfill efficiency standards despite potential performance setbacks. However, it is essential to recognize that even minor design adjustments could impact product performance, influencing energy consumption throughout the product’s lifespan.
Decision Time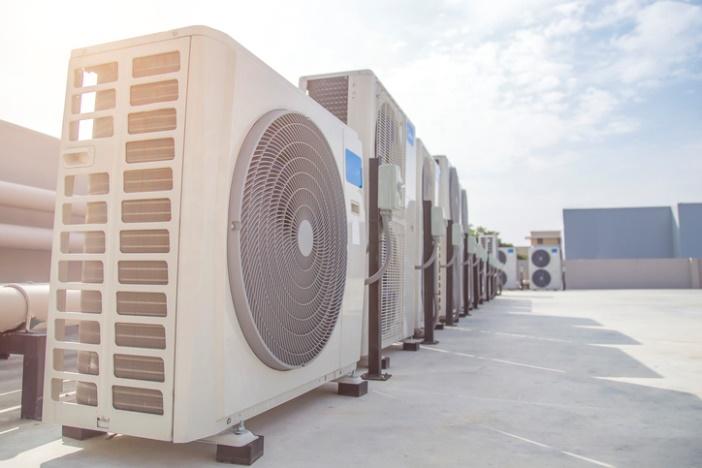
The decision-making process concerning adopting new refrigerants to replace R410A involves careful consideration. There are ongoing discussions regarding the accessibility of these alternatives, and OEMs have yet to fully endorse R454B.
Additionally, there exists a divergence of perspectives regarding the utilization of R32, which, while approved and utilized in Asia, encounters more regulatory hurdles in the US. Notably, R454B incorporates R32 as one of its constituents, offering a slightly lower Global Warming Potential (GWP) than other options.
OEMs, such as Whirlpool, partner with OTS R&D Inc., in collaboration with the Copper Development Association, to redesign alternative evaporator and condenser designs as they transition to low-GWP refrigerants. For a partnership with Whirlpool, OTS R&D Inc. successfully identified an optimal design that surpasses the baseline coil in all measurable parameters by meticulously evaluating over 55,000 evaporator and condenser models. The resulting design modifications demonstrate how small-diameter copper has superior performance in heat transfer applications.
In the case study, we explain the proposed modifications and illustrate how implementing small-diameter copper tubing enhances heat pump performance.
You can find out more here if you want to learn more about what a partnership with the Copper Development Association and OTS R&D for research and development entails.